FGI Creates FREE Online PDH Credit Program
The FGI has created a program that will offer engineers one (1.0) Professional Development Hour (PDH) of credit for each FGI webinar that is viewed from the FGI Online Webinar Library. The FGI currently has thirteen (13) webinars in its online library and is offering an additional four (4) live webinars this year: CCR Regulations and Policy (August 6), Temporary Landfill Covers (September 10), Lightweight Aggregate (October 15), and Geomembrane Wrinkles (November 12). A PDH certificate will be issued to anyone who attends a live webinar or views a pre-recorded webinar in its entirety. Each live webinar will be added to the FGI's online library after the initial airing date.
For more information or to view the list of webinars, please visit: www.fabricatedgeomembrane.com/resources/webinar-gallery
To learn more/register for the August 6, 2019 webinar on CCR Policy and Regulations, please visit: https://register.gotowebinar.com/register/4561903830197164300
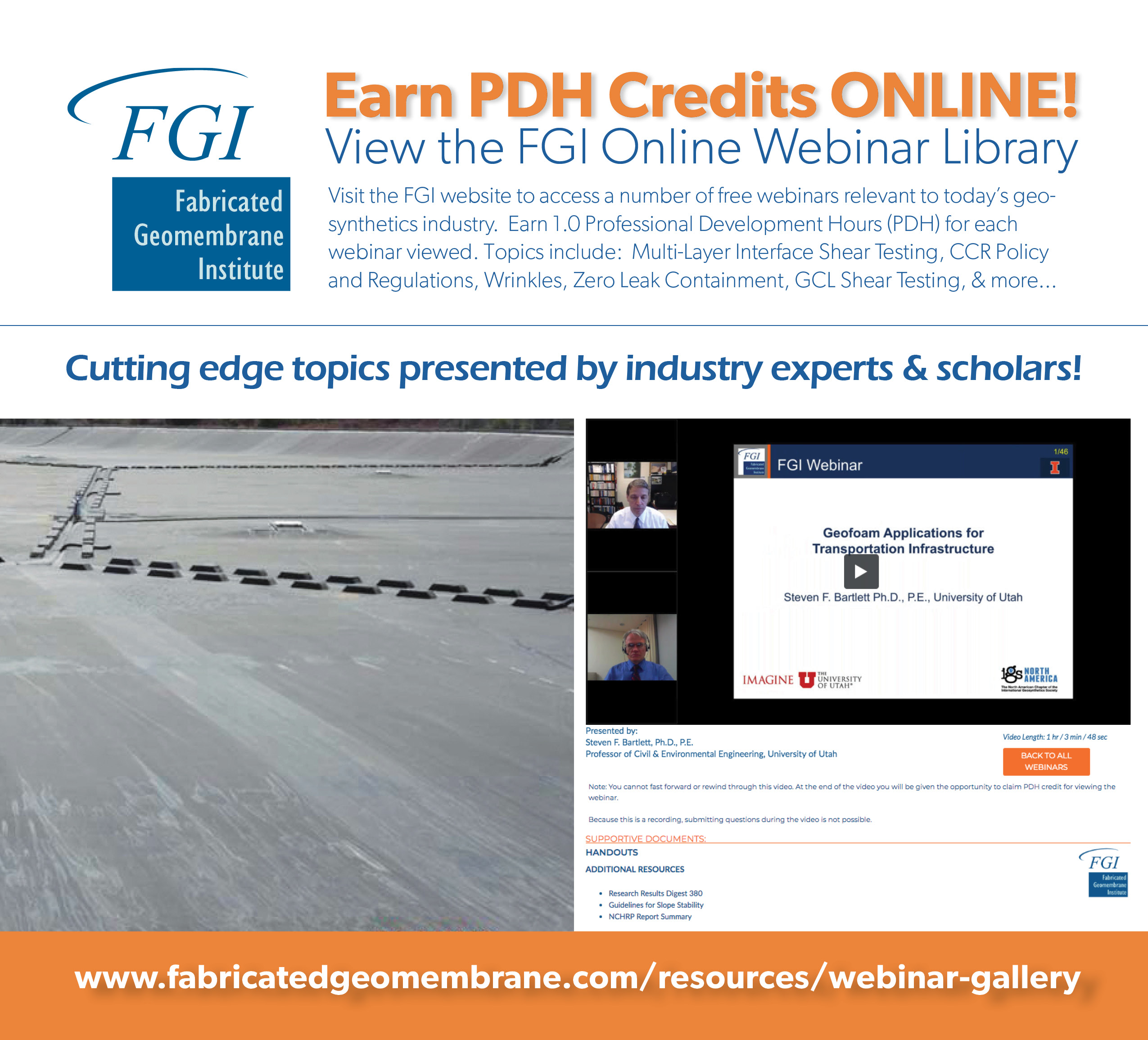
FGI To Offer Coal Combustion Residuals Short Course
The Fabricated Geomembrane Institute is offering a one day short course on Coal Combustion Residuals (CCRs): Current Regulations and Solutions. The short course will take place on Wednesday, November 6, 2019 at the Center City Building near the University of North Carolina Charlotte campus. Attendees will gain a broad knowledge of current and emerging CCR regulations, local experience managing CCRs, and the advantages of using geosynthetics to manage and dispose of CCRs. Course attendees will earn seven (7.0) PDHs. Lunch and break refreshments will be provided. The short course is offered in collaboration with S&ME, Wood, University of North Carolina Charlotte (UNCC) and the University of Illinois at Urbana-Champaign. The short course will feature dynamic presentations from representatives of Consumers Energy, Duke Energy, American Electric Power, UNCC, The Ohio State University, Wind Defender, Wood, TRI, DemTech, Leister and S&ME.
For more information or to register, please visit: https://www.geosynthetics-ccrs-charlotte-2019.eventbrite.com
Early bird registration discount ends October 15, 2019.
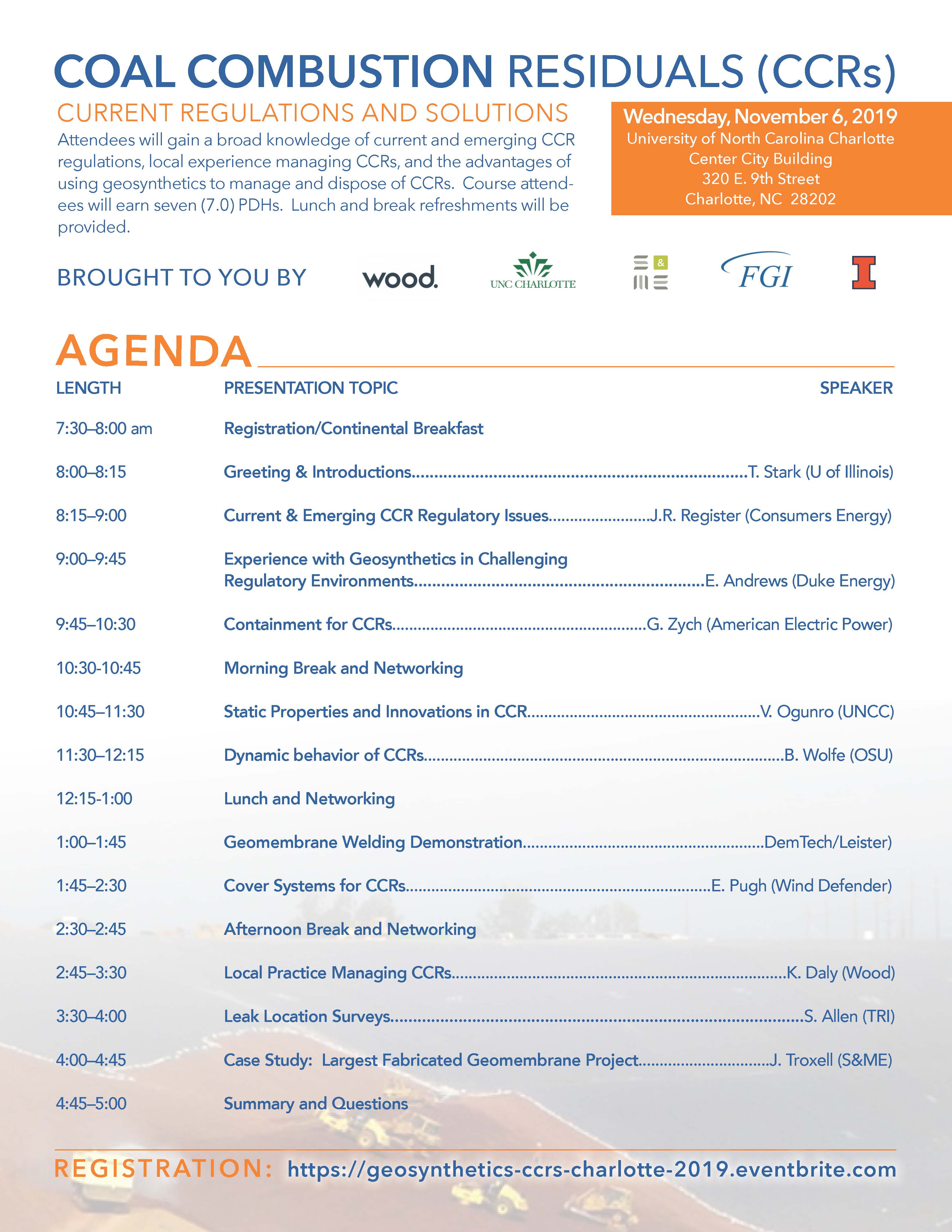
FGI Welcomes Poly Fab LLC
The Fabricated Geomembrane Institute (FGI) is pleased to welcome its newest fabricator/installer member, Poly Fab LLC (www.polyfabllc.com). Poly Fab LLC was established to supply step and panel geomembranes to the water transfer energy companies in several of the shale project areas in Texas, New Mexico, Colorado and Oklahoma. PolyFab’s primary lining products are fabricated polyethylene geomembranes and non-woven felt pads. Their FGI liaison is Enrique Saavedra, Business Development Manager, who can be reached at sales@polyfabllc.com. Please help us welcome PolyFab LLC to the FGI!!!!
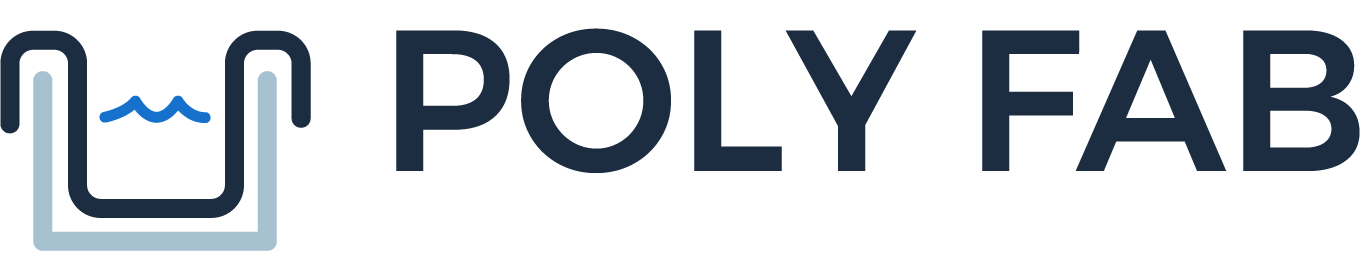
FGI Publishes Article on Elvaloy Nomenclature in Geosythetics
June/July 2019
Geosynthetics Magazine
By E. Silva and T. D. Stark
Since the first flexible membrane liner (FML) was used as part of an environmental liner system, the geomembrane industry has always looked for innovative solutions to environmental containment applications. Although there have been many innovations over the last fifty (50) years, one of the most significant is the introduction of ketone ethylene ester (KEE), which is a solid plasticizer. KEE is available under the Elvaloy® trade or product name and is used to plasticize PVC geomembranes as discussed in detail below.
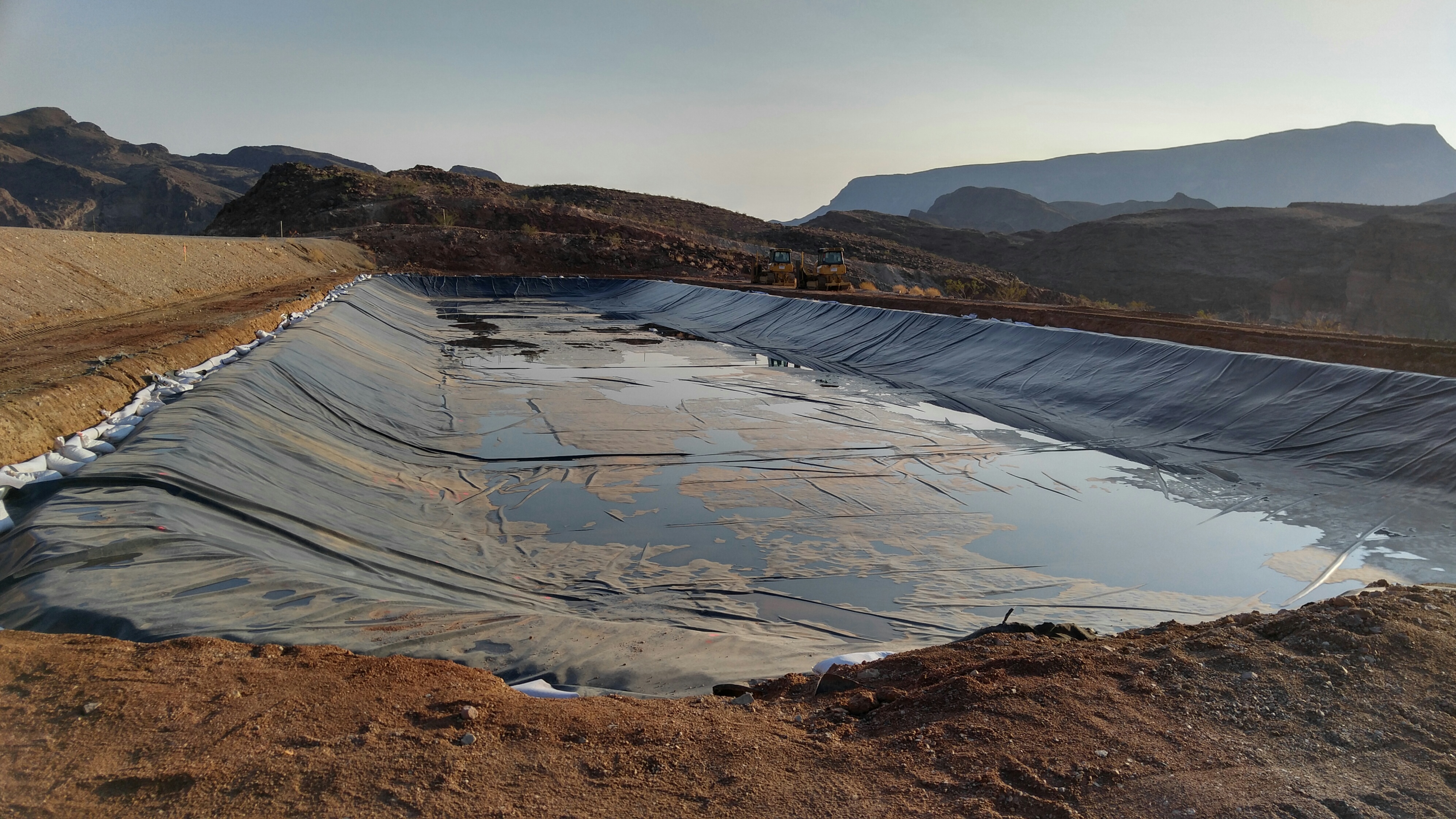
FGI Records Two New Testing Videos
The Fabricated Geomembrane Institute (FGI) at the University of Illinois at Urbana-Champaign has created a library of Geomembrane Test Method Videos that explain various factory and field test methods. Testing videos available to view/download include demonstrations on how to measure the following: thickness, tensile strength, dimensional stability, seam shear and peel strength, and brittleness.
The FGI has recently recorded two new testing videos, as part of the Geomembrane Test Method Library on the FGI website: ASTM D1204 Dimensional Stability and ASTM D1790 Brittleness Temperature of Plastic Sheeting by Impact.
In addition to these two testing videos, the FGI has recorded the following testing videos available to view/download:
ASTM D7408 Seam Peel Strength
ASTM D882 Tensile Properties Geomembranes
ASTM D7408 Seam Shear Strength
ASTM D5994 Thickness Textured Geomembrane
ASTM D5199 Procedure B Thickness Smooth Geomembrane
Download/View Testing Videos Here: https://www.fabricatedgeomembrane.com/resources/video-gallery
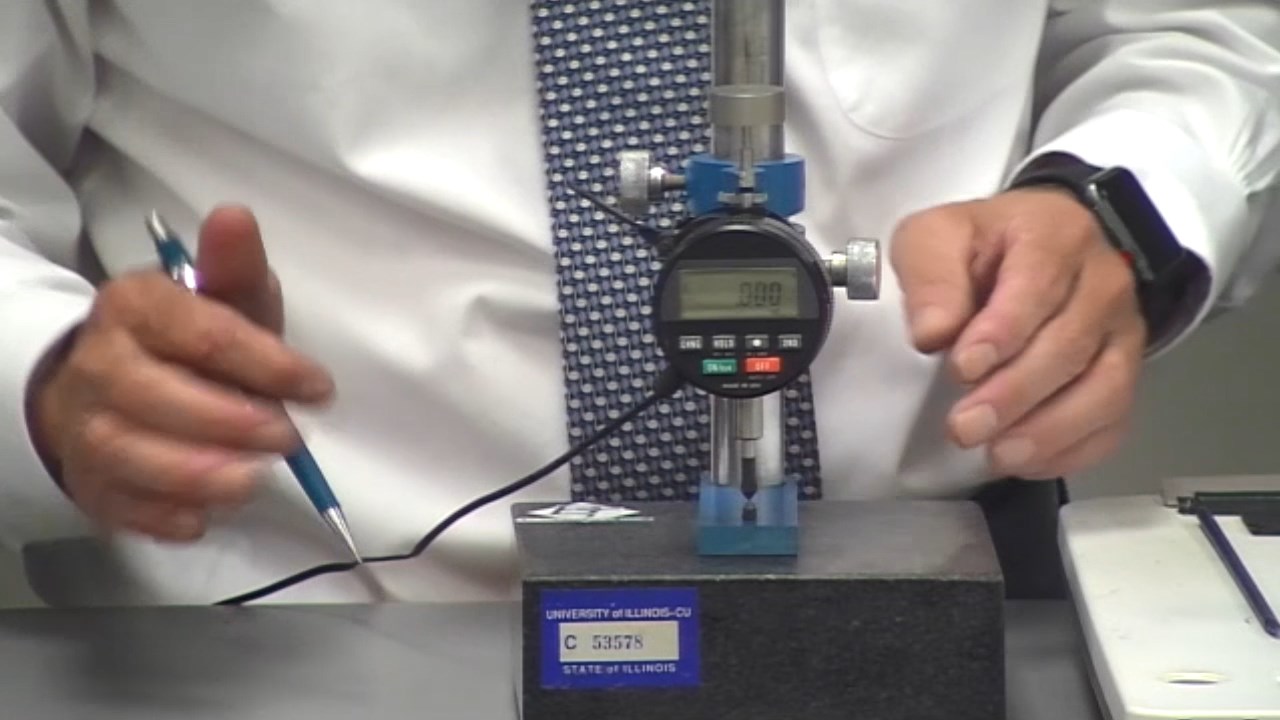
FGI Welcomes Tonkin + Taylor
The Fabricated Geomembrane Institute (FGI) is pleased to welcome its newest consultant member– New Zealand’s leading environmental and engineering consultancy, Tonkin +Taylor. Head-quartered in Auckland (NZ), Tonkin + Taylor operates throughout the South Pacific, Australasia and Southern Asian region. The company is 100% employee owned and operated and is highly experienced and skilled at delivering significant solid waste, transport,utilities, coastal management, flood protection and climate change adaptation capital works programs. Their FGI liaison is senior civil/environmental engineer Jonathan Shamrock, JShamrock@tonkintaylor.co.nz. Please help us welcome Tonkin + Taylor to the FGI!!!!

Timothy Stark Participates in ACIGS International Speaker Series
The Australasian Chapter of the International Geosynthetics Society (ACIGS) recently hosted their International Speakers Series in Australia and New Zealand.
The New Zealand seminar was held in Auckland on Monday, February 18, 2019 and presented by Timothy Stark, Professor of Geotechnical Engineering in the Department of Civil and Environmental Engineering at the University of Illinois at Urbana–Champaign. Important lessons were learned by the 40 delegates attending the seminar about current best practice use of geosynthetics for embankment and lined waste containment facilities based on current research and from analysis of real life case studies of failures.
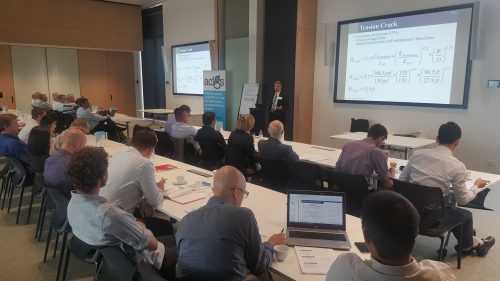
Professor Stark presented on the following topics:
- Geosynthetic Interface Testing and Selection for Static and Seismic Stability where he explained the importance of interface shear testing for geosynthetic lined slopes, the correct test methods to use, and the interpretation of these test results.
- Vertical Geosynthetic Drain Analyses for Embankment Failure on Soft Soil were he presented case histories illustrating design parameters for prefabricated vertical (wick) drains and their practical implications for stability of embankments.
- Seismic Stability of a Geosynthetic Lined Slope where he presented, using a case study, the importance of designing for peak and residual shear strength on landfill liner systems base and side slopes respectively and the appropriate factors of safety to use for the design cases.
- Elevated Temperatures in Waste Containment Facilities and Effect on Geosynthetic Service Life and Facility Design where he presented on the causes and implications for geosynthetic service life of elevated temperatures in waste containment facilities.
For complete article, please visit: www.geosyntheticssociety.org/acigs-international-speakers-series/
FGI PRESENTS ENGINEERING INNOVATION FOR OUTSTANDING PROJECT AWARD TO HULL & ASSOCIATES, INC.
The Fabricated Geomembrane Institute (FGI) at the University of Illinois at Urbana-Champaign presented two (2) Fabricated Geomembrane Engineering Innovation Awards during its biennial membership meeting in Houston, Texas on February 12, 2019 at the 2019 Geosynthetics Conference. The 2019 Engineering Innovation Award for Outstanding Fabricated Geomembrane Project was presented to Hull& Associates, Inc. (see Figure 1) for the Montour Ash Landfill-Contact Water Basin Project.
Coal Combustion Residuals (CCRs) are by products of the combustion of coal at power plants owned by utility companies and power producers. CCRs are typically stored within surface impoundments as wet slurry or into landfills as dry CCRs. One type of CCR, fly ash, can be used for beneficial use in concrete. In some cases, fly ash may be extracted from dry landfills for beneficial use. In preparation for the harvesting of fly ash from the existing closed landfill at the Montour Power Plant, a contact water basin was constructed in 2018 downstream of the landfill. The contact water basin was constructed to manage contact water that would be generated when surface water contacts exposed fly ash during harvesting operations. The initial permit application for the basin included a composite geosynthetic liner system consisting of, from bottom to top: an engineering subgrade with underdrain system, geosynthetic clay liner (GCL),60 mil textured high density polyethylene (HDPE) geomembrane, non-woven cushion geotextile, and a protective stone layer.
Hull & Associates, Inc. (Toledo, OH) prepared the basin design to manage the runoff anticipated from a 25-year/24-hour storm event, while also providing temporary storage of any sediment-laden material within the basin. Prior to construction of the composite liner system, Owens Corning and CQA Solutions approached Hull to propose the use of a RhinoMat Reinforced Composite Geomembrane (RCG) as a moisture barrier between the underdrain and GCL to aid the construction process due to the extensive precipitation that was occurring in the area. To ensure that the RhinoMat andGCL interface would not pose an interface friction and slope stability risk and would meet permit requirements, Hull initiated laboratory shear testing of the material prior to construction. The testing indicated that the materials would be stable with the 4H:1V side slopes of the basin. The contact water basin design is approximately 1.9 acres in area, with 4H:1V side slopes, and a depth of roughly 11 feet. Factory fabrication of the RhinoMat geomembrane resulted in four panels being created,three of which were identical size, and relatively square in shape (160 ft. x170 ft.). The fourth panel was fabricated into a 120 ft. by 155 ft. rectangle.Panels were designed for optimal placement and deployment direction for ease of installation based on the proposed basin configuration and to minimize field seaming and testing.
Installation of the RhinoMat geomembrane began at approximately 8:00 a.m. on the morning of July 21, 2018. All four panels were deployed and placed in the anchor trenches before noon on that day, using a crew of approximately eleven (11) people. A 0.5-inch rainstorm began at approximately 12:00 p.m. that afternoon and prevented any welding the rest of that day. However, the deployed RhinoMat protected the engineered subgrade, and prevented damage to the previously exposed underdrain system. On July 22, 2018, the basin was partially full from rainfall. Water had to be pumped from the basin to ensure that panel edges were dry enough to complete the three connection field seams. Once these seams were complete, they were non-destructively tested, and boots were installed around the two inlet pipes. RhinoMat installation was deemed complete on the afternoon of July 22, 2019, just a few hours prior to a historic rainfall event.
The week of July 23, 2018 brought over 11 inches of rainfall to the Washingtonville, PA area, causing historic flooding and damage to roads, bridges, and flood control structures. Rapid installation of the fabricated RhinoMat geomembrane on July 21 and 22 provided protection for the engineered subgrade and underdrain in the basin, which would have otherwise been damaged to the point of required reconstruction, and over of $100,000 in rework. The RhinoMat withstood the rainfall, and served as a high-performance moisture barrier within the composite liner section of the basin design. This is an example of the benefits of the high quality and rapid deployment of fabricated geomembranes and how fabricated geomembranes can help solve construction challenges, while also meeting design intent and permit requirements.
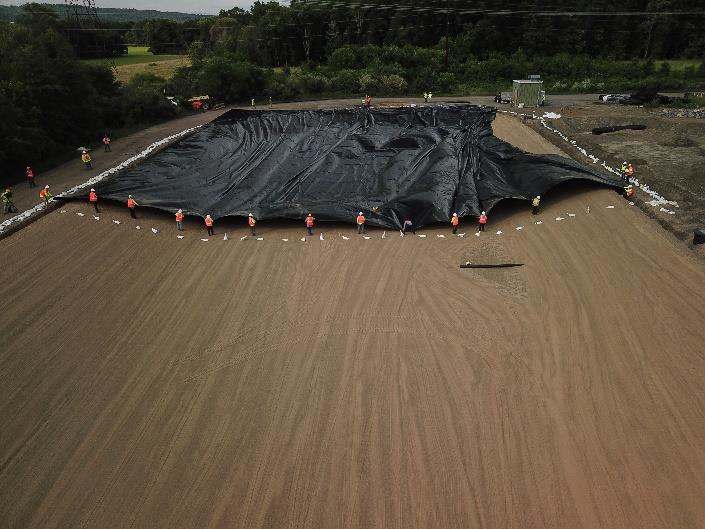
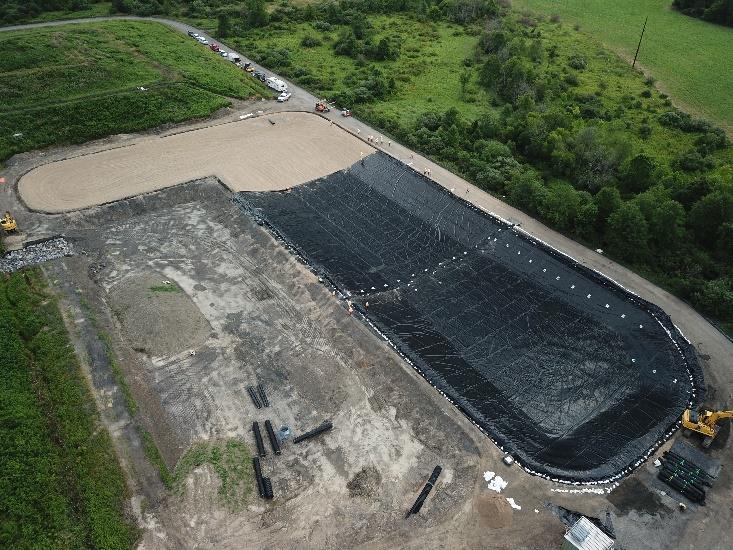
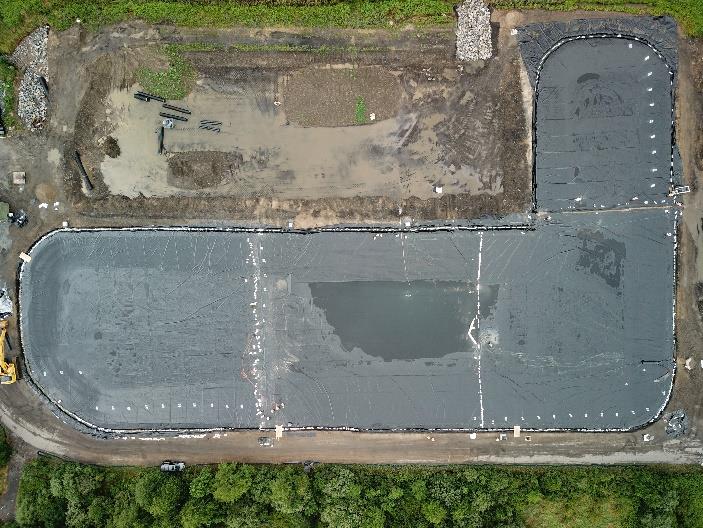
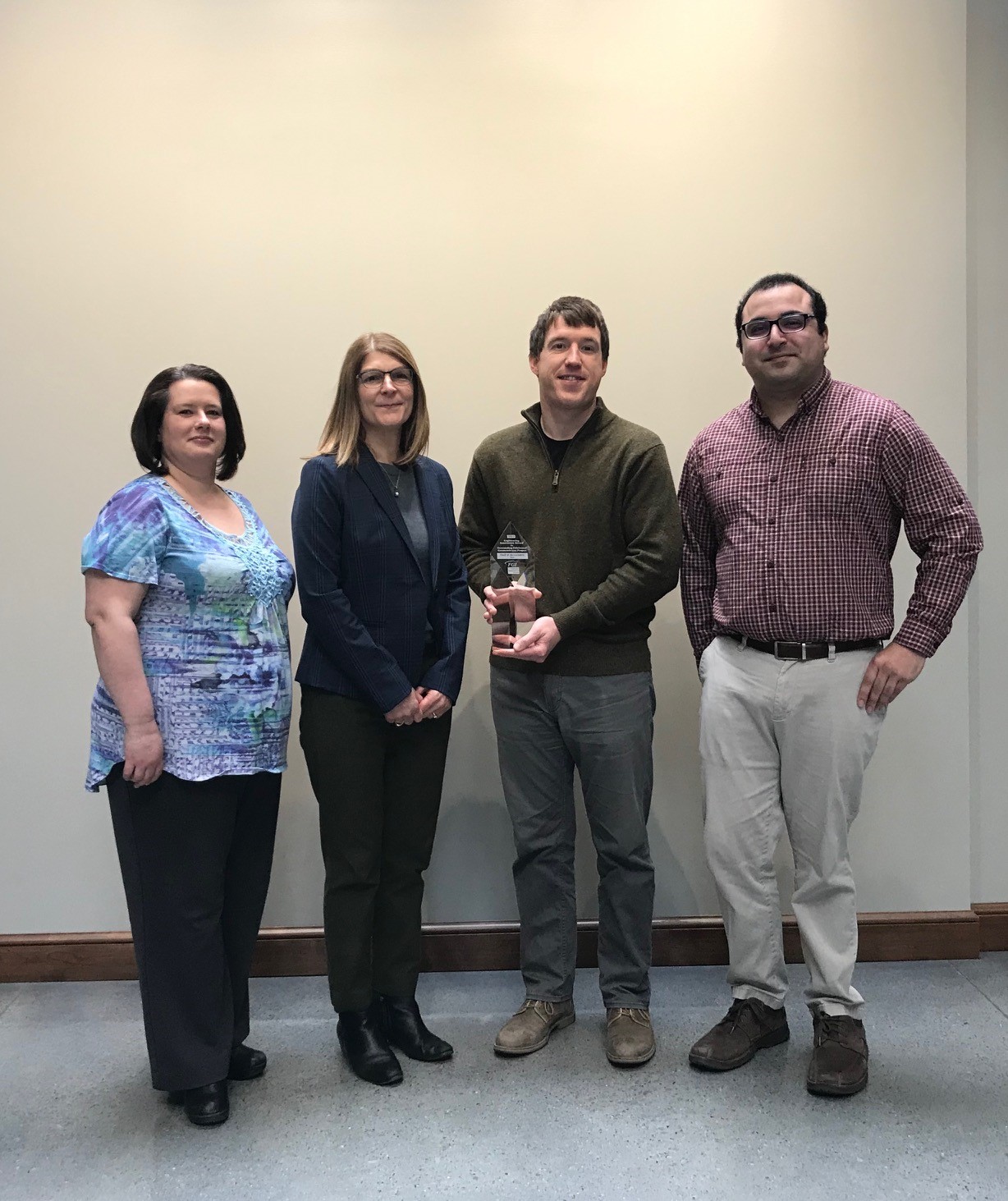
FGI Welcomes TenCate Geosynthetics
The Fabricated Geomembrane Institute(FGI) is pleased to welcome its newest manufacturer member, TenCate Geosynthetics (www. tencategeo.us). TenCate is headquartered in Pendergrass, Georgia and serves the market globally with two commercial divisions – TenCate Geosynthetics and TenCate Industrial Fabrics. TenCate specializes in providing the highest quality geosynthetics products and solutions that enhance the world’s infrastructure, protect the environment, and conserve natural resources. Their FGI liaison is Brian Baillie, Commercial Director – Environmental Infrastructure Group, who can be reached at b.baillie@tencategeo.com. Please help us welcome TenCate to the FGI!!!!
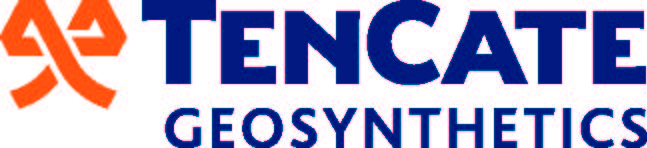
FGI PRESENTS ENGINEERING INNOVATION AWARD TO J.C. YORK, P.E.
The Fabricated Geomembrane Institute (FGI) at the University of Illinois at Urbana-Champaign presented two (2) Fabricated Geomembrane Engineering Innovation Awards during its biennial membership meeting in Houston, Texas on 12 February, 2019 during the 2019 Geosynthetics Conference. The 2019 Engineering Innovation Award for Specifying Fabricated Geomembranes was presented to J.C. York of J& T Consulting, Inc. (see Figure 1) for the Fort Lupton Terminal Reservoir and the Taproot Water Storage Pond Projects.
The Fort Lupton Terminal Reservoir is a raw water storage facility that was built to serve North Denver and surrounding cities. The Northern Colorado Water Conservancy delivers source water to the city of Fort Lupton and Tri-State through a pipeline that terminates at Fort Lupton’s Water Treatment Facility. The pipeline requires general maintenance annually, which results in temporarily closing the pipeline. During pipeline maintenance or shutdown, no source water can be provided to the City or Tri-State. As a result, a water storage storage reservoir with a two (2) to six (6) week capacity had to be created and lined with a geomembrane to limit leakage. This reservoir liner system also had to be designed for a rapid drawdown (larger water discharge volumes) due to demand or operational reasons. This proved challenging because there are few geomembranes that can withstand the design rapid drawdown and provide the factors of safety required by the State of Colorado Dam Safety Rules and Regulations. The challenging water storage reservoir was designed by J&T Consulting with civil operations performed by Sema Construction. The geosynthetics portion of the project is comprised of a 12 inch thick (0.3 m) gravel layer and the following liner system from bottom to top: an 8 ounce nonwoven geotextile underlayment, 36 mil thick double sided textured reinforced polyethylene (RPE) geomembrane, and an 8 ounce cushion nonwoven geotextile that served as protection from the 18 inches of cover soil.
To accelerate construction, increase quality, and make construction more modular and predictable, the RPE geomembrane was pre-fabricated, which reduced field welding by approximately 80%. Figure 2 shows some of the pre-fabricated panels being deployed. The project involved considerable creative details due to the inflow and outflow structures and requirements,as well as spillway (see Figure 3). The nonwoven geotextiles were also pre-fabricated to accelerate construction. In addition to the standard quality assurance(QA) procedures for a bottom liner system, a third party leak location survey was performed aftercover soil placement (see Figure 4) to minimize leakage. This survey found nomajor defects to the liner system even after cover soil placement. This was confirmation of the success of the project by J & T Consulting, Raven Industries (manufacturer, fabricator, and installer), and Sema Construction.
The Taproot Storage Pond is a fresh water storage pond intended to service oil fields in Northeastern Colorado. This pond also had a rapid drawdown design issue because the drilling process utilizes a large volume of water for the oil/gas well development. The bottom liner system consists of a geomembrane placed on the existing fine-grained soils that had to be ballasted to prevent failure during rapid drawdown. Also designed by J & T Consulting, with civil operations performed by Northern Colorado Constructors, this project posed many challenges from a design and construction standpoint. A geomembrane that could not only withstand the harsh chemical and windy conditions of the eastern Colorado plains, but also could be installed in a short installation window, was needed. Raven Industries’ 45 mil thick RPE geomembrane (see Figure 5) was used because of its durability and longevity in harsh conditions, as well as designing of an integrated ballast system for the slopes that would ensure that the high winds and rapid drawdown would not affect liner system integrity.
The FGI Engineering Innovation Award provides recognition for engineer(s) who have creatively used fabricated geomembranes to successfully fulfill a client/owner’s needs including, technical requirements, scheduling, and budget.
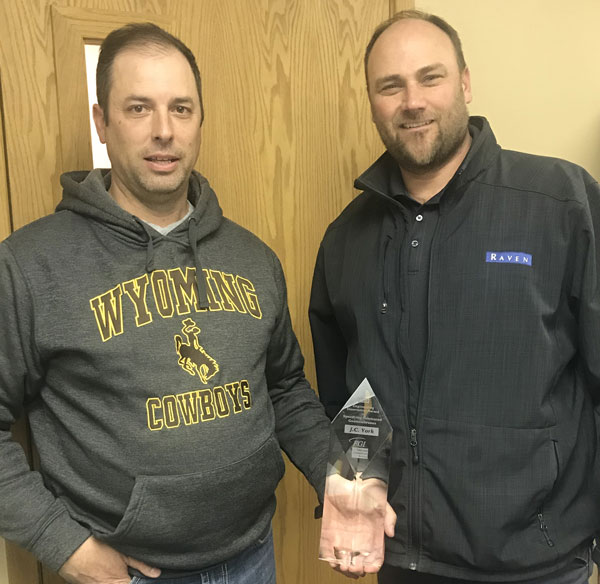
J.C. York (left) receiving FGI Engineering Award from Patrick Elliott, FGI President